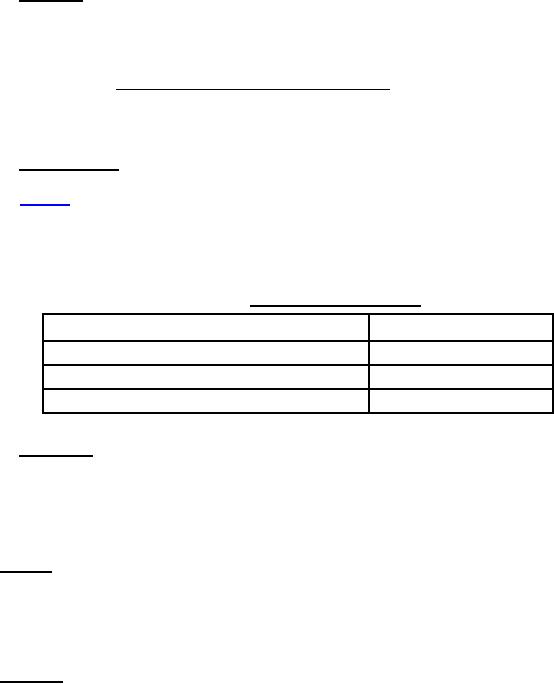
MIL-DTL-24705B(SH)
4.6.12 Expansion. A sample of the insert material (see 3.1) shall be placed into an oven with the temperature
held constant at 80 to 85 °C for not less than 1 hour. Before the test, the sample shall he measured for its actual
dimensions. After the test, the sample dimensions shall be measured after the sample has been cooled to ambient
temperature. The percentage change in volume shall he calculated as follows:
(Volume after test) (Volume before test)
Expansion percentage
=
× 100
(Volume before test)
Insert material shall meet the requirements specified in 3.5.10.
4.6.13 Fluid immersion. A sample insert material shall be placed face down in a container containing
approximately 13 mm (one half inch) of fluid for not less than 2 hours. The fluids and temperatures shall be as
specified in table VI. The samples shall then be removed, blotted to remove excess fluid, and suspended in air at
room temperature for not less than 3½, nor more than 4½ hours. Each sample shall then be tested again as specified
in 4.6.10. Test shall be repeated for each specified fluid. Insert material shall meet the requirements specified in
TABLE VI. Test fluids and temperatures.
Fluid
Test temperatures
Fuel oil (as specified in MIL-DTL-16884)
Ambient
Hydraulic fluid (as specified in MIL-PRF-17331)
Ambient
Coolant (Monsanto Coolapol 25, or equal)
20 to 25 °C
4.6.14 IR signature. A sample of the insert material (see 3.1) shall be examined and analyzed to determine its
IR signature. The procedure used shall be of a type normally used by commercial test laboratories and shall be
included along with the results of the examination and analysis in the test report. A copy of the IR record shall be
kept by the manufacturer for comparison against results of subsequent inspection (Group C) tests. The results of
subsequent inspections submitted to NAVSEA shall include a copy of the original IR signature for comparison
purposes.
4.7 Toxicity. The penetrators shall be evaluated by the Navy and Marine Corps Public Health Center
(NMCPHC) using the administrative Health Hazard Assessment (HHA). Sufficient data to permit an HHA of the
product shall be provided by the manufacturer/distributor to the NMCPHC. To obtain current technical information
requirements specified by the NMCPHC, see 6.6.
5. PACKAGING
5.1 Packaging. For acquisition purposes, the packaging requirements shall be as specified in the contract or
order (see 6.2). When packaging of materiel is to be performed by DoD or in-house contractor personnel, these
personnel need to contact the responsible packaging activity to ascertain packaging requirements. Packaging
requirements are maintained by the Inventory Control Point's packaging activities within the Military Service or
Defense Agency, or within the military service's system commands. Packaging data retrieval is available from the
managing Military Department's or Defense Agency's automated packaging files, CD-ROM products, or by
contacting the responsible packaging activity.
6. NOTES
(This section contains information of a general or explanatory nature that may be helpful, but is not
mandatory.)
13
For Parts Inquires submit RFQ to Parts Hangar, Inc.
© Copyright 2015 Integrated Publishing, Inc.
A Service Disabled Veteran Owned Small Business